
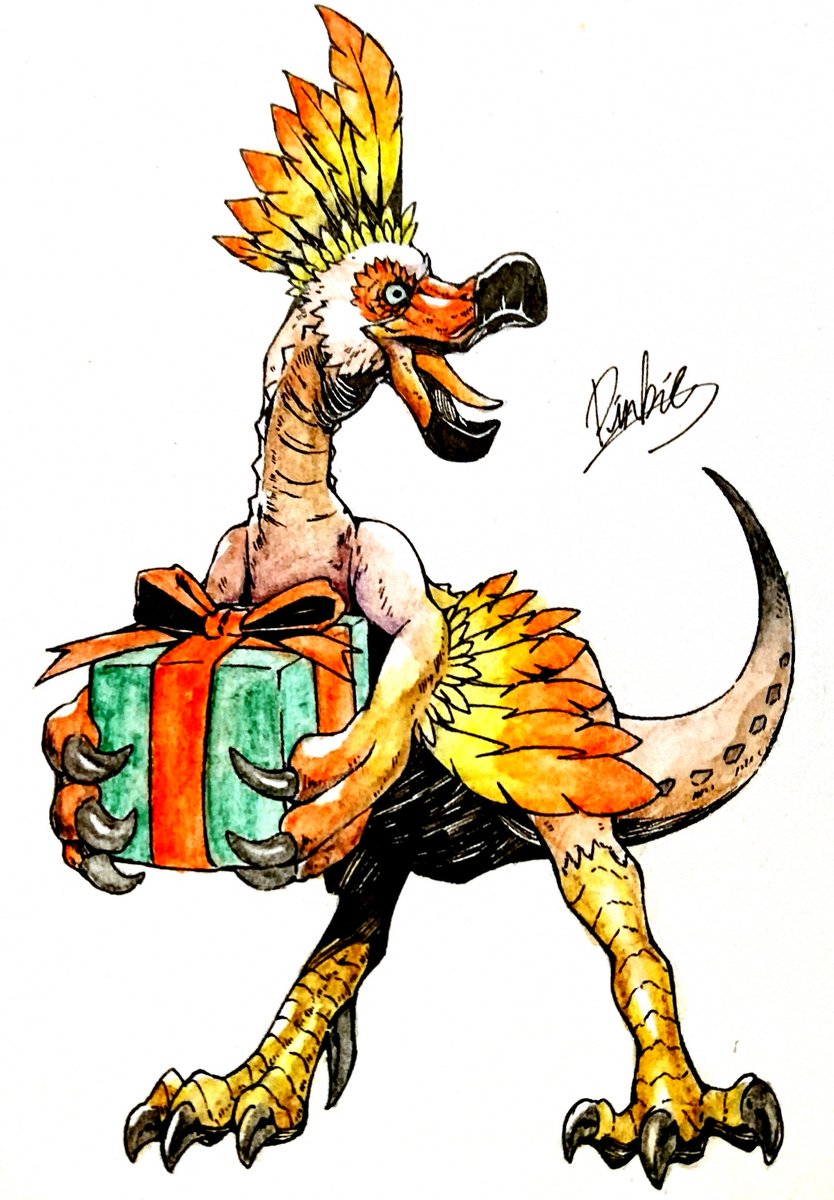
Sadly I dream bigger than my 3d printer but not to worry that is what super glue is for. Then using the revolve and offset commands I made a series of evenly spaced holes around the base of the horn. To make the sewing work I placed a hole in the base of the horn. I was going to be attaching these horns to fabric and the easiest way I could think of was to sew them on. Now that my horn was editable it was time to get to work. Again I turned to an article on Autodesk's website. Now that my awesome horn mesh was in Fusion360 I had to change it to a BRep to make it editable. Once I had my 3d model looking the way I wanted it was time to import it into Autodesk's Fusion360 program. On the bright side that means that this is an achievable beginner project because I am a beginner! The tip I will share is that I found starting with an imported plane worked best for me. I'm not going to go into detail on the sculpting process because I pretty much just read this article by Autodesk and smashed my head into my screen until I was happy with the way the horn looked. Meshmixer is a program by Autodesk that lets you mash up meshes as well as sculpt in the 3d space. If you just want to skip to the printing I am including the STL files I created for printing. After looking at a lot of Beefalo pictures and my Beefalo plushies it was time to dive into Meshmixer.
